Plasma supports mobility-related changes in the battery industry
Explore the remarkable capabilities of this eco-friendly and highly efficient technology live at Battery Show and Electric & Hybrid Vehicle Technology Expo 2024!
Visit us at The Battery Show North America in the German Pavilion at booth 3930 or at Electric & Hybrid Vehicle Technology Expo at booth 2911 and be impressed by the potential of plasma treatment as a pretreatment for all types of batteries.
Changing mobility means that demand for high-powered EV batteries is growing rapidly. New production lines are being built all over the world that are geared to mass production. When looking for the optimal battery, range and fast charging are important criteria. To achieve this, the battery needs to be well insulated, structurally bonded and thermally conductive.
This is where Plasmatreat comes in:
Plasma technology is the key technology for microfine cleaning, surface activation and nano-coating of a wide range of materials. This technology supports various production steps and offers a number of advantages over other processes.
Excellent use can be made of this in the various steps of high-performance battery manufacturing and can be achieved with Plasmatreat's systems and equipment for inline plasma activation to reliable bond and seal housings or for cleaning and coating of batteries.
Why should you take a closer look at plasma technology?
Surface treatment with Openair-Plasma® is based on a simple physical principle: When energy is supplied, the states of matter change. Thus, solid becomes liquid and liquid becomes gaseous. If further energy is now added to a gas, e.g. air, it is ionized and changes to the high-energy plasma state. If the ionized gas meets a surface, its properties change.
Plasma, as the fourth state of matter -besides solid, liquid, and gas-, offers numerous advantages:
- Environmentally friendly: Our production is VOC-free and the technology is CO2-neutral
- Easy to integrate: easy integration into existing processes
- Quality and reliability: Improved manufacturing quality and longer battery life
- High cost-effectiveness: high process efficiency thanks to high process speed and low reject rates, use of more favourable materials thanks to flexible material selection
Learn more at The Battery Show at our booth 3930 or visit us at booth 2911 at Electric & Hybrid Vehicle Technology Expo and see for yourself!
You can't make it to the fair? Get in touch with us here!
How does plasma work?
Openair-Plasma® is generated with electricity and compressed air and is even CO2-neutral when green energy is used. All plasma processes are solvent-free, contribute to the environmental balance and can be integrated into existing production lines.Dry surface treatment with Openair-Plasma® can be carried out in a fully automated process, as an environmentally friendly alternative to harmful chemical processes. Here, the need for additional pre-treatments with chemical primers is eliminated during the activation and fine cleaning of various surfaces prior to bonding, coating, painting, or sealing. Modern, solvent-free or water-based adhesives, paints, and varnishes can then be used. This significantly reduces the emission of VOCs in production.


Plasma in battery manufacturing
Plasma technology is used for all kinds of batteries: prismatic, cylindrical and pouch cells. The areas of application are extremely wide. For example, optimization of electrical insulation can be achieved via plasma cleaning prior to coating or the covering of individual cells with PET film. In cell-to-cell bonding, meaning adhesion of individual cells to the battery module, plasma treatment activates the cell surfaces after application of the coating or the film covering, thereby improving adhesion and thus thermal conductivity. The adhesiveness of structural bonding in a battery module, e.g. of the side walls, can be increased through plasma treatment of the components.
Process automation with battery standard equipment
At the Battery Show North America 2024, we will be presenting plasma treatment for various battery types and sizes in a special system that can be easily integrated into the production line: The Plasma Treatment Unit (PTU) equipped with a robot and our system components. Our generator, different jets (for example RD1004, RD2005) and our Openair-Plasma® process monitoring PCU illustrate the extensive product portfolio. With a special focus on the Plasma Control Unit (PCU), we will show you how comprehensive process monitoring and control can meet high requirements and support digitalised production processes.

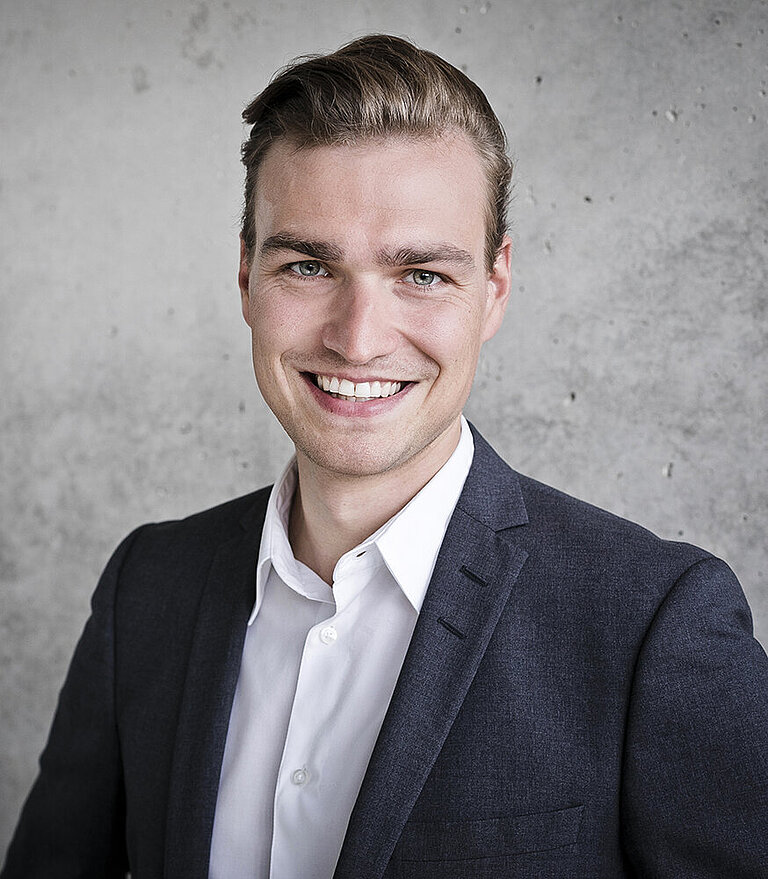
With the wide range of different nozzles and generators and the different handling systems we use for plasma treatment, we can offer our customers exactly the solution they need for their particular process and production environment."
Our worldwide Sales and Service is there for you - where ever you are!

With our network of research and development centers, subsidiaries and commercial agencies around the world, we are always present wherever our expert knowledge and experience in the field of individual surface treatment is in demand. We offer you local and individual support in your time zone and language. This ensures that our advice is focused on your challenge, that we understand it and that together we find a solution that is tailored to your individual needs.
You can't be at the trade fair but still want to test the effect of plasma on your own materials? Our Book-a-Demo makes it possible!
Book a customised live demonstration, follow the handling and plasma treatment of your sample, get answers to your specific questions, see what plasma can do and find the best solution for your application together with our plasma experts near you.
We are ready for your challenge!
You can experience a compact introduction to atmospheric plasma technology at The Battery Show North America in the German Pavilion at booth 3930 or at Electric & Hybrid Vehicle Technology Expo at booth 2911. Discover various equipment and systems for demonstrating Openair-Plasma® surface treatment: using a XPlanar, we will demonstrate the treatment of various battery cells and housings.
On our Livetable we will show you the benefits of cleaning battery cells before the electrical isolation and you will learn about the activation of PET films or PET spray coatings. Also you have the chance to test the materials you have brought along for their suitability for plasma treatment.
Our atmospheric plasma technology can be a game changer with regards to adhesion characteristics, substrate substitutes or functionalization of surfaces.
Give it a try: Our experienced application engineers are looking forward to working with you to find the best solution for your use case.
Book an appointment with our colleagues at the booth and visit us on site!